All-in-one form, transformerless
Industrial Application
Commercial Use
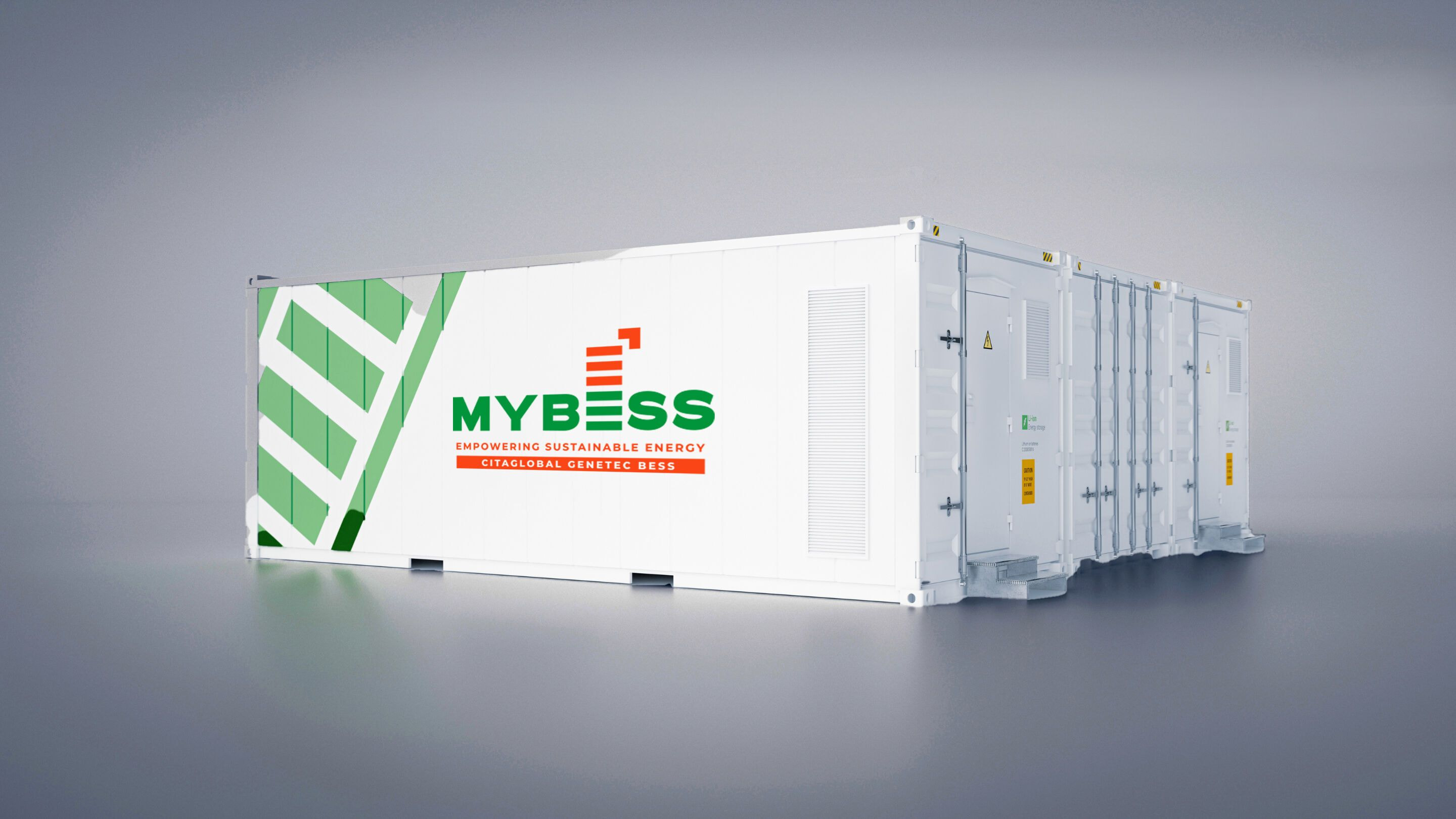
FAQ
Find out more.
Lithium Iron Phosphate (“LFP”) batteries are a type of lithium-ion battery that use iron phosphate as the cathode material. The chemical composition of LFP batteries is highly stable, has a long lifespan, and is more resistant to heat degradation than nickel-cobalt (NCA) batteries. LFP batteries are also known for their high energy density, good performance at high temperatures, and are generally considered easier to recycle compared to other types of batteries.
SOH - Indicates the level of degradation and remaining capacity of the battery.
SOC - Represent the remaining available battery capacity.
DOD - Indicates the capacity that is discharged from a fully charged battery.
5 years for battery cluster and battery management system
3 years for all other components
The product life cycle of Battery Energy Storage Systems (BESS) refers to the number of times a battery can be charged and discharged before its capacity degrades to a specified level. Here's a breakdown:
Cycle Life: The cycle life of a BESS refers to the number of complete charge and discharge cycles it can undergo before its capacity degrades to a specified level. This degradation occurs gradually over time due to factors such as chemical reactions, electrode degradation, and electrolyte decomposition.
Factors Affecting Cycle Life:
Depth of Discharge (DoD): The extent to which the battery is discharged during each cycle affects its cycle life. Shallower discharge cycles typically result in longer overall cycle life.
Temperature: Operating the battery at higher temperatures can accelerate degradation and reduce cycle life.
Charge and Discharge Rate: Charging or discharging the battery at high rates can also accelerate degradation and reduce cycle life.
State of Charge (SoC): Keeping the battery at high or low states of charge for extended periods can affect cycle life.
Chemistry and Design: Different Lithium-ion chemistries and battery designs have varying cycle life characteristics.
Specified End-of-Life Criteria: The cycle life of a BESS is typically defined based on specific end-of-life criteria, such as when the battery's capacity degrades to a certain percentage of its original capacity (e.g., 80% or 70%).
Lifetime Expectancy: At the operating condition of charge and discharge rate at 0.5C, the expected life cycle of Lithium-ion BESS can be exceeding 8000 cycles or more than 15 years of lifetime. It is designed to have longer cycle life and higher durability, making them suitable for applications requiring extended operational lifetimes.
The delivery lead time for our Battery Energy Storage Systems (BESS) typically takes about 4 - 6 months, here's a breakdown of each phase:
Order Processing: After receiving a purchase order, we initiate the order processing phase. This involves reviewing the order details, specifications, and any customization requirements specified by the customer.
Component Procurement: We procure the necessary components and materials required to assemble the BESS system. This may include lithium-ion battery pack, battery management systems, power conversion system, cooling systems, enclosures, transformer and other auxiliary equipment.
Manufacturing and Assembly: Once the components are procured, the manufacturing and assembly process begins. This involves assembling the various components into a complete BESS system according to the customer's specifications. Quality control checks are conducted throughout the manufacturing process to ensure that the final product meets the required standards and specifications.
Testing and Quality Assurance: After assembly, the BESS undergoes rigorous testing and quality assurance procedures to ensure that it functions correctly and meets performance specifications. This may include electrical testing, functional testing, safety testing, and performance validation tests.
Shipping and Logistics: Once the BESS has passed all quality assurance tests, it is prepared for shipping. Depending on the size and weight of the BESS system, it may be shipped ground freight or sea freight. Logistics arrangements are made to ensure timely delivery to the customer's location.
Installation and Commissioning: Upon delivery, our engineers and technicians handle the installation and commissioning of the BESS, integrating with the existing electrical infrastructure, configuring settings, and conducting initial performance tests to ensure proper operation
Battery energy storage systems (BESS) require regular operation and maintenance to ensure optimal performance and longevity.
However, our BESS technology allows for a more autonomous and self-monitoring system, meaning less maintenance for the user. With our Bess system, the user can rest easy knowing that the equipment is constantly checking and adjusting itself to ensure optimal performance.
This not only saves time and money on maintenance costs but also increases the lifespan of the equipment.
In addition to self-monitoring, the Bess system can also be configured to communicate with a centralized control system or the cloud, allowing for remote monitoring and control.
This means that even if the users are not on-site, they can still monitor the performance of the Bess system and make adjustments as needed, ensuring a more efficient and reliable operation. Generally, here are some key considerations for the operation and maintenance of a battery energy storage system:
- Monitoring: Continuous monitoring of the system is essential to detect any anomalies or performance issues. This includes monitoring the battery state of charge, voltage levels, temperature, and overall system efficiency. Automated monitoring systems can provide real-time data and alerts for efficient operation.
- State of Charge (SoC) Management: Proper management of the battery's state of charge is crucial. Regularly monitoring and controlling the SoC helps prevent overcharging or deep discharging, which can degrade battery performance and reduce its lifespan. Implementing appropriate charge and discharge algorithms can help optimize SoC management.
- Temperature Control: Battery temperature significantly affects its performance and lifespan. Monitoring and controlling the battery temperature within the recommended operating range is essential. Our BESS system is considered a reliable liquid cooling system and ensures proper ventilation in the battery installation area.
- Regular Inspections: Periodic visual inspections of the battery system, including the physical condition of batteries, electrical connections, and protective enclosures, should be conducted. Any signs of damage, corrosion, or loose connections should be addressed promptly.
- Cleaning and Maintenance: Keeping the battery system clean and free from debris is important. Regularly inspecting and cleaning battery terminals, connectors, and cooling systems helps maintain proper electrical contact and cooling efficiency.
- Battery Testing and Replacement: Over time, battery performance may degrade, leading to reduced capacity or increased internal resistance. Regular battery testing, including capacity tests and impedance measurements, can help identify potential issues. If necessary, the entire battery pack may need to be replaced. We could also consider an augmentation plan to increase the storage capacity to offset the degradation.
- Firmware and Software Updates: Battery management systems (BMS) and Energy management systems (EMS) often require firmware updates to improve performance, efficiency, and system integration. Regularly checking for updates with the latest software revisions and security patches is important.
In general, preventive maintenance should be performed on a regular basis to ensure the safe and efficient operation of the BESS.
We recommend that preventive maintenance be performed at least twice a year. During these maintenances, the batteries and power electronics are inspected, cleaned, and tested to ensure that they are operating properly.
The control system is also checked to ensure that it is communicating with other components of the energy system and that it is regulating the charge and discharge of the batteries correctly.
In addition to annual maintenance, more frequent inspections and testing may be necessary depending on the operating conditions of the BESS. For example, if the BESS is operating in a harsh environment with high temperatures or humidity levels, more frequent maintenance may be necessary to prevent issues such as overheating or corrosion.
It is important to follow our recommended maintenance schedule and to work with experienced technicians who can perform the necessary maintenance tasks safely and effectively.
By performing regular preventive maintenance, issues can be identified and addressed before they become major problems, ensuring the safe and efficient operation of the BESS.
Liquid cooling is a method used in Battery Energy Storage Systems (BESS) to regulate the temperature of the batteries, thereby optimizing their performance and enhancing their lifespan. In this method, a liquid coolant circulates through a network of channels or pipes, absorbing heat from the batteries and carrying it away to be dissipated elsewhere, such as through a heat exchanger.
Here's how the liquid cooling method typically works in a BESS:
Coolant Circulation System: A closed-loop system is employed to circulate the coolant throughout the battery modules or packs. Pumps are used to push the coolant through the system, while valves and controls regulate the flow rate and distribution.
Coolant: The coolant used in liquid cooling systems for BESS is usually a mixture of water and ethylene glycol. This coolant has excellent thermal properties, allowing it to efficiently absorb heat from the batteries while also provides antifreeze properties.
Cooling Channels: Within the battery modules or packs, there are channels or passages through which the coolant flows. These channels are designed to come into close contact with the battery cells or modules, ensuring effective heat transfer.
Heat Exchanger: After absorbing heat from the batteries, the warm coolant is circulated to a heat exchanger, where it releases its heat to the surrounding environment through ambient air to dissipate the heat.
Temperature Control: Sensors and control systems monitor the temperature of the batteries and adjust the flow rate of the coolant as needed to maintain optimal operating temperatures. This helps prevent overheating, which can degrade battery performance and reduce their lifespan.
Liquid cooling offers several advantages for BESS:
Improved Thermal Management: Liquid cooling provides more efficient heat dissipation compared to air cooling, allowing for better thermal management of the batteries.
Enhanced Performance: By maintaining optimal operating temperatures, liquid cooling can help ensure consistent performance and efficiency of the batteries.
Extended Lifespan: Effective thermal management can help prolong the lifespan of the batteries by reducing stress and degradation caused by temperature extremes.
Safety: Proper temperature control helps mitigate the risk of thermal runaway and other safety hazards associated with overheating batteries.
Overall, liquid cooling is a key technology used in BESS to ensure reliable and efficient operation while maximizing the longevity of the battery system.
In a Battery Energy Storage System (BESS), the fire suppression system is a critical safety feature designed to prevent and extinguish fires that may occur within the battery enclosure or adjacent to it. The fire suppression system typically consists of several components:
Detection System: This part of the system is responsible for identifying any signs of fire or overheating within the battery system. It includes smoke detectors, heat sensors, or other types of detectors specifically designed to monitor conditions associated with battery fires.
Alarm System: Once a potential fire is detected, the alarm system activates to alert personnel or authorities about the situation. This alert ensures that appropriate actions can be taken promptly to mitigate the risk of fire spreading.
Suppression Agents: Fire suppression agents are substances used to extinguish fires. Common agents used in BESS fire suppression systems include water, foam, dry chemicals, or specialized gases like Novec 1230 or HFC-227. The choice of suppression agent depends on various factors such as the type of batteries used, the size of the installation, and environmental considerations.
Delivery System: The delivery system is responsible for dispersing the suppression agent to the location of the fire. This can involve sprinkler systems, nozzles, or other distribution methods strategically placed within the battery enclosure or surrounding area.
Control System: The control system manages the activation and operation of the fire suppression system based on inputs from the detection system. It ensures that the suppression agent is deployed effectively and in a timely manner to contain and extinguish the fire.
Overall, the fire suppression system in a BESS is a crucial safety measure to minimize the risk of fire-related incidents and protect both the equipment and personnel in the vicinity.
From 8 footer (215kWh) to double unit of 20 footer (3.7MWh)
The design lifetime of MYBESS is 20 years, after which the battery will reach the end-of-life. As battery is considered as hazardous material, a proper decommissioning plan help to minimize the environmental impact. At the time the projects cease to operate, the decommissioning activities includes removal and recycling of the BESS containers and associated battery packs. With proper removal and arrangement of the battery packs, it can then be arranged and transported to a recycling centre for raw material recovery and recycling.
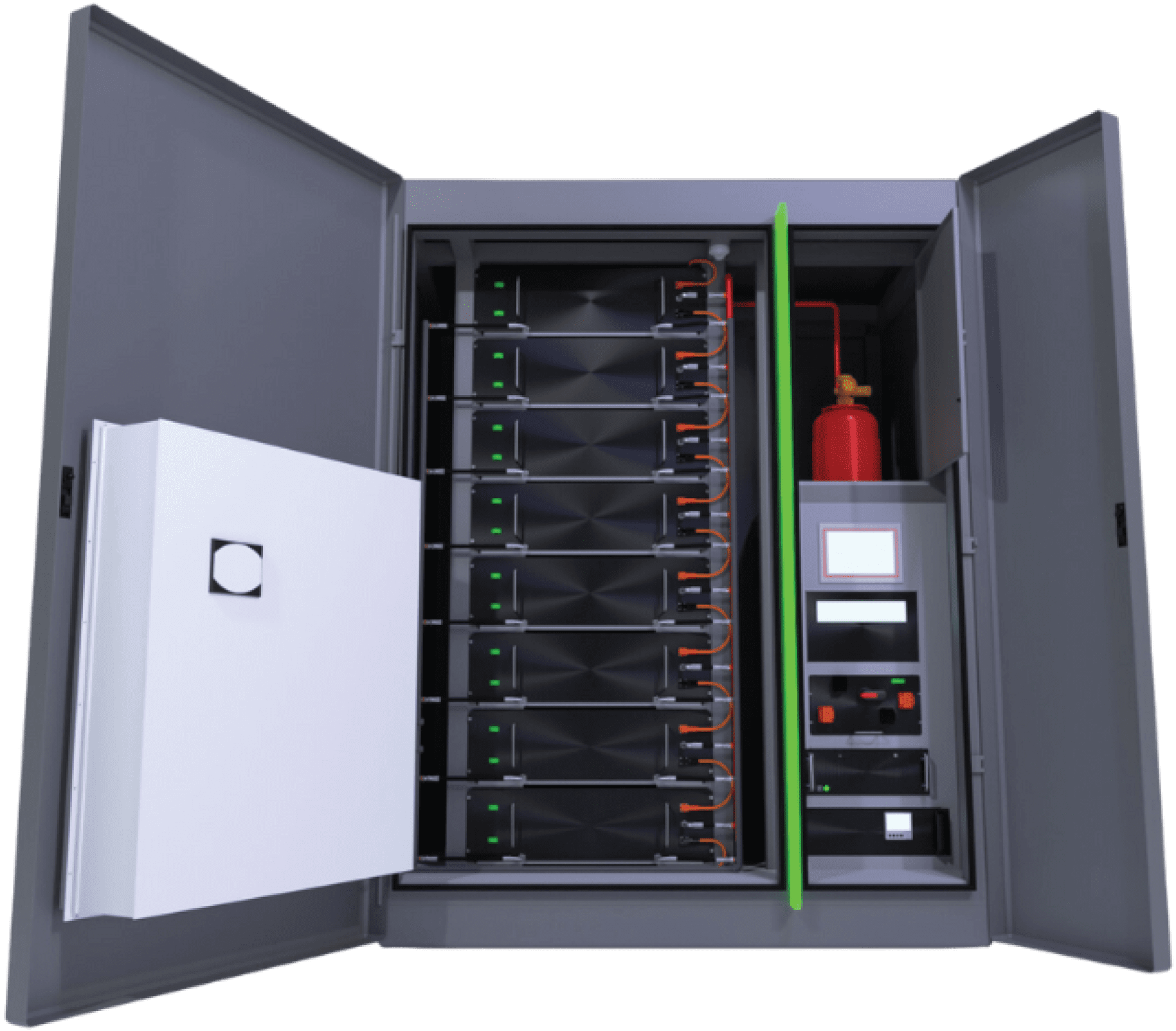
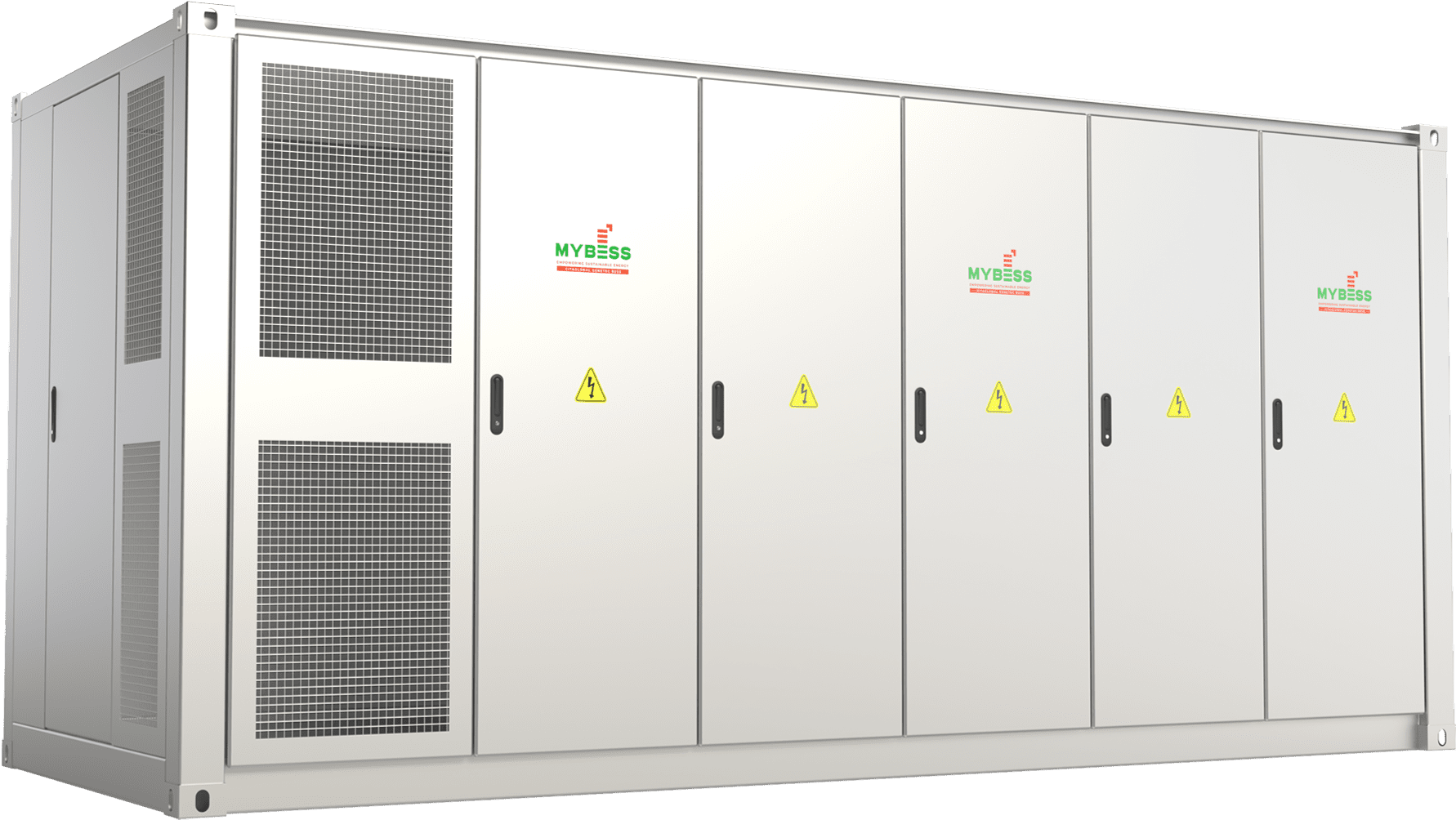